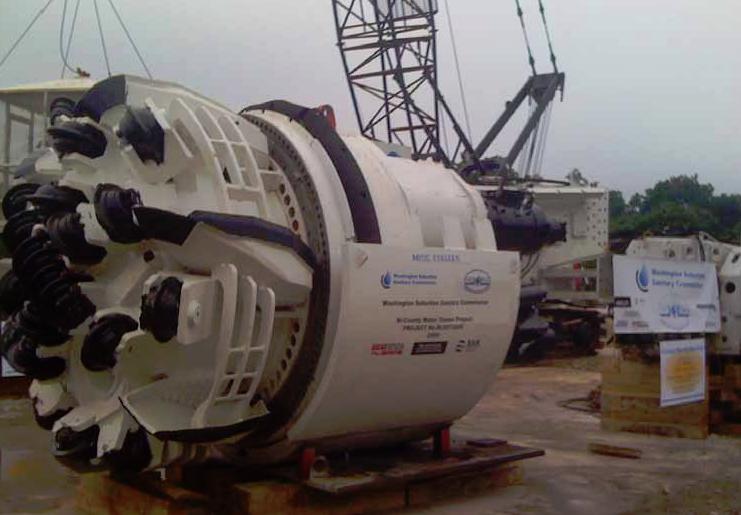
Tunnel boring can be hard work, but it doesn’t come much harder than on this Maryland project by Oscar Renda Contracting, as Alan Swaby learns.
There are gophers busy under the suburbs of Silver Spring, Maryland, but they’re not doing any harm. Instead, they’re busy nibbling away the rock, ready to construct a vital link in the Washington Suburban Sanitary Commission (WSSC) water system.
Known as the Bi-County Water Tunnel, the 5.3-mile tunnel will eventually connect two existing water mains in Montgomery County and Prince George’s County. It’s a $168 million safety precaution to provide a redundant water tunnel in case a nearby tunnel should fail.
The Bi-County water supply main project was first identified in the late 1960s. Since that time, WSSC and the planning agencies of the two counties involved have been monitoring water system performance, water pressure, demand and growth patterns to determine an appropriate project implementation.
In 2004 they judged the time was right to begin work so that it would be complete by the decade’s end. Without it, WSSC couldn’t be sure of providing a daily reliable water supply. Throw in emergencies such as fires, droughts or, heaven forbid, another hurricane like Isabel, and the risk of disruption becomes even greater.
Had this project not gone ahead, the community would have begun to notice the effects of low water pressure. Should this drop below 30 pounds per square inch, there is an immediate impact on the ability of the fire department to provide effective protection. At the same time, residents would notice a decrease in their plumbing performance should several faucets be open at the same time. Consequently, serious planning for the pipeline began in 2004, and contracts were awarded for the drilling of the tunnel in 2009.
The firm chosen to do the work, Oscar Renda Contracting (ORC), is from Roanoke, Texas, and despite being in business since 1974 and probably holding the number one position for water treatment plants in the Southwest, it’s only in last six years or so that it has begun to make a mark farther afield.
ORC is one of those “successful immigrant” stories. The young Oscar arrived with his family in 1956 under provisions of the Refugee Act, and immediately began chasing the American Dream. After a childhood juggling education and part-time jobs, he was well equipped to launch ORC in 1974 while holding down two other full-time jobs.
“This work ethic,” says regional manager Tim Winn, supervising the Bi-County project, “underlies everything the company does. It found success in the early years by taking on the most difficult and challenging projects and made a reputation by completing them regardless of their financial outcome.”
On that basis, then, the Bi-County pipeline has been awarded to the right guys, as it is a far-from-straightforward project. WSSC could have specified an open-cut pipeline involving excavation and burial of a pipeline no deeper than 20 feet underground. However, such an approach would have required a working area at least 75 feet wide along the entire length of the pipeline. The noise, vibrations and additional vehicular traffic would have caused considerable disruption in what is already a highly congested residential locality.
Instead, the decision was taken to go underground, but this brought its own set of problems. The main access point for the tunnel is from a two-acre site just off the Washington inter-loop. Here a 36-foot shaft has been sunk 180 feet deep at the center point of the 28,000-foot-long tunnel. “Once we got to the bottom,” says Winn, “the rock was solid, but at around 50 feet we encountered a lot of groundwater that needed to be sealed off before we could continue.”
Saying that the rock is solid is something of an understatement. It’s solid granite rated at 20,000 psi or, in other words, five times harder than concrete. ORC has brought in as partner the specialist tunneling company Southland Contracting, Inc., which utilizes a 10-foot-diameter Robbins tunnel-boring machine. Even then, Miss Colleen—as the tunnel borer has been affectionately named—has had to be beefed up considerably. Horsepower was increased 50 percent to 1,250 and the hydraulics similarly boosted to cope with the constant strain of a 20-hour-per-day, six-day-per-week boring schedule.
At the start of each shift, the cutting heads have to be examined for wear and replaced if necessary. Then the borer goes to work, chipping tiny fragments of the granite face, which are then conveyed back to muck carriers taking spoil out to the surface.
“Getting enough ventilation through this relatively small tunnel is a significant challenge,” says Winn. “Normally there would be additional shafts for ventilation, but we have only the three shafts effectively 2 ½ miles apart. That has called for a much more robust ventilation system to keep the guys safe.”
The one advantage of this type of granite is that it is solid, removing the need for significant tunnel supports except in only around 5 or 10 percent of its length where it passes through fault zones. Once the 14 months of laser-guided boring is complete, the next stage will be to lower and install an 84-inch steel pipe in 50-foot-long sections that then have to be butt-welded and grouted into place. The pipe has a concrete lining to give it corrosion protection, and the final stage of the build is to line over the inside of the welded joints, giving it seamless protection.
There’s been some disruption for residents, and occasionally there’s a report of the earth moving as low-impact blasting takes place, but WSSC has gone out of its way to minimize the impact on residents, who will of course be much happier in October next year when their water supply is so much more assured than it is today.